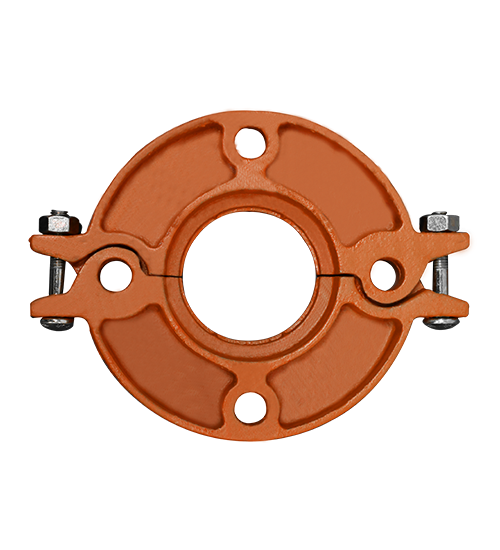
Mastering Connections: A Deep Dive into the Various Types of Mechanical Coupling Flanges
In the intricate tapestry of engineering, mechanical coupling flanges emerge as unsung heroes, providing the backbone for seamless connections within complex systems. This article delves into the world of mechanical coupling flanges, exploring the diverse types that play a pivotal role in ensuring efficiency, reliability, and precision in engineering applications.
I. Defining Mechanical Coupling Flanges:
A. Core Purpose and Functionality:
1. Enabling Connection Between Pipes and Equipment
2. Facilitating Easy Assembly and Disassembly
B. Importance in Piping Systems:
1. Ensuring Leak-Free and Secure Joints
2. Contributing to System Integrity
II. Types of Mechanical Coupling Flanges:
A. Rigid Flanges:
1. Stiff and Stable Connections
2. Common in High-Stress Environments
B. Flexible Flanges:
1. Accommodating Misalignments and Vibrations
2. Applications in Systems with Dynamic Loads
C. Slip-On Coupling Flanges:
1. Quick and Easy Installation
2. Suitable for Low-Pressure Applications
D. Grooved Coupling Flanges:
1. Groove and Gasket System for Sealing
2. Versatility in Applications
E. Clamp-Type Coupling Flanges:
1. Bolted Clamp for Secure Connections
2. Ideal for Temporary Joints and Repairs
III. Material Selection and Considerations:
A. Stainless Steel Coupling Flanges:
1. Corrosion Resistance in Harsh Environments
2. Common in Chemical and Marine Industries
B. Carbon Steel Coupling Flanges:
1. Strength and Durability
2. Applications in Industrial Pipelines
C. Alloy Coupling Flanges:
1. Tailoring Material Properties for Specific Applications
2. Aerospace and High-Temperature Environments
IV. Design Considerations:
A. Pressure and Temperature Ratings:
1. Matching Flange Ratings with System Requirements
2. Ensuring Safety and Reliability
B. Gasket Selection and Compatibility:
1. Choosing Appropriate Gasket Materials
2. Sealing Solutions for Various Fluids
V. Applications Across Industries:
A. Oil and Gas Sector:
1. Coupling Flanges in Pipeline Systems
2. Rigidity in Offshore and Onshore Applications
B. Water Treatment and Distribution:
1. Leak-Free Connections in Water Pipelines
2. Applications in Municipal Infrastructure
C. Chemical Processing:
1. Compatibility with Corrosive Chemicals
2. Reliability in Chemical Manufacturing Plants
VI. Installation and Maintenance Best Practices:
A. Proper Alignment and Torque:
1. Ensuring Tight and Secure Connections
2. Preventing Gasket Compression Issues
B. Periodic Inspection and Monitoring:
1. Detecting Signs of Wear and Corrosion
2. Proactive Maintenance for Longevity
VII. Emerging Trends and Innovations:
A. Smart Coupling Flanges:
1. IoT Integration for Condition Monitoring
2. Predictive Maintenance for Enhanced Reliability
B. Environmentally Friendly Materials:
1. Sustainable and Recyclable Flange Options
2. Aligning with Green Engineering Practices
Conclusion:
As we navigate the complexities of fluid systems and industrial infrastructure, understanding the different types of mechanical coupling flanges becomes paramount. This article serves as a comprehensive guide, shedding light on the nuances of each type and emphasizing their crucial role in fostering resilient and efficient connections in the diverse landscape of engineering.