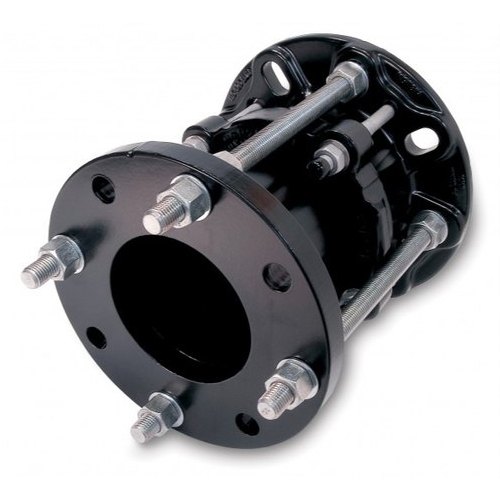
Forging Connections: Unraveling the Distinctions Between Welding and Riveting in Structural Joinery
In the realm of structural engineering and fabrication, the choice between welding and riveting is a critical decision that significantly impacts the integrity and performance of assembled components. This comprehensive exploration will delve into the nuanced differences between welding and riveting, examining the processes, applications, and considerations that guide engineers in selecting the optimal method for joining materials.
I. Understanding Welding: The Fusion of Strength
1. Welding Process Overview:
Welding is a fabrication process that involves the fusion of materials through the application of heat. The process melts the base metals, allowing them to mix and solidify into a strong joint. This method is renowned for creating seamless connections that exhibit exceptional strength and structural integrity.
2. Types of Welding Joints:
Various types of welding joints exist, including butt joints, lap joints, and fillet joints. Each type is chosen based on the specific requirements of the joint and the structural demands of the application.
II. Understanding Riveting: The Art of Mechanical Fastening
1. Riveting Process Overview:
Riveting is a mechanical fastening process that involves the use of metal rivets to join materials. The process entails driving a rivet through aligned holes in the materials and then deforming the protruding end to create a secure connection. Riveting is known for its reliability and structural stability.
2. Types of Riveted Joints:
Common types of riveted joints include lap joints, butt joints, and double cover butt joints. The selection depends on factors such as the thickness of materials, load-bearing requirements, and aesthetic considerations.
III. Differences in Structural Integrity: Strength vs. Rigidity
1. Welding Strength:
Welded joints exhibit exceptional strength as the materials are fused, creating a homogeneous connection. Welding is particularly advantageous in applications where the joint must withstand high loads, making it a preferred choice in heavy-duty industries like construction and shipbuilding.
2. Riveting Rigidity:
Riveted joints offer rigidity and stability due to the mechanical interlocking of the rivet within the materials. While riveting may not match the strength of welding, it excels in applications where flexibility and movement are not primary concerns.
IV. Advantages and Limitations of Welding: Precision and Permanence
1. Welding Advantages:
Welding provides a seamless and permanent connection, eliminating the need for additional fasteners. It is suitable for applications requiring precision, minimal aesthetic disruption, and a high level of structural reliability.
2. Welding Limitations:
Welding may pose challenges in terms of distortion, heat-affected zones, and the need for skilled labor. Additionally, it is not easily reversible, making modifications or repairs more complex compared to riveting.
V. Advantages and Limitations of Riveting: Versatility and Accessibility
1. Riveting Advantages:
Riveting is versatile and accessible, requiring less specialized equipment than welding. It is suitable for field installations and repairs and allows for easier disassembly and modifications when compared to welding.
2. Riveting Limitations:
Riveting may introduce additional weight due to the use of multiple rivets, and the process can be more time-consuming than welding. The visible rivet heads may also impact aesthetics in applications where a seamless appearance is desired.
VI. Application Considerations: Choosing the Right Method
1. Structural Applications:
Welding is often preferred in heavy structural applications, such as bridges, buildings, and industrial machinery, where the joint must withstand significant loads and stresses.
2. Aerospace and Automotive:
In industries like aerospace and automotive, where weight considerations are critical, riveting may be favored for its ability to provide strength while minimizing the added weight associated with welding.
VII. Innovation and Future Trends: Pushing the Boundaries
1. Hybrid Joining Technologies:
Innovation in joining technologies explores hybrid methods that combine the strengths of both welding and riveting. These approaches aim to create joints that leverage the precision of welding and the versatility of riveting.
2. Advanced Materials and Processes:
Advancements in materials science and manufacturing processes continue to push the boundaries of what is achievable with both welding and riveting. From high-strength alloys to automated robotic welding, the future promises even more sophisticated and efficient joining solutions.
VIII. Conclusion: Forging the Future of Structural Joinery
In conclusion, the choice between welding and riveting is a nuanced decision that hinges on the specific requirements of the application, material characteristics, and structural considerations. Engineers must weigh the advantages and limitations of each method to ensure optimal performance and longevity. This exploration serves as a guide for navigating the complexities of structural joinery, forging the future with a deep understanding of the distinctions between welding and riveting in the realm of engineering.