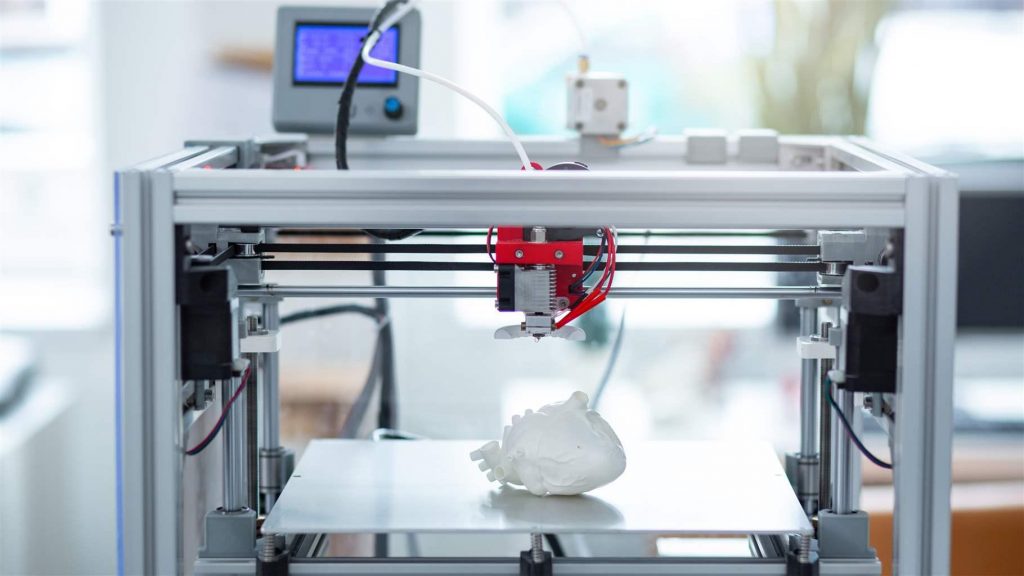
Pushing the Boundaries: Exploring the Minimum Thickness for 3D Printing
In the rapidly evolving world of 3D printing, one question that often arises is, "What is the thinnest you should 3D print?" This query delves into the realm of precision and feasibility, as well as the limitations of current technology. In this article, we will explore the factors that influence the minimum thickness for 3D printing and discuss the practical implications for various industries. So, let's dive into the fascinating world of ultra-thin 3D printing!
- Understanding the Basics of 3D Printing:
Before we delve into the thinnest possible prints, let's briefly recap the fundamentals of 3D printing. 3D printing, also known as additive manufacturing, is a process that builds objects layer by layer using a digital model. It offers unprecedented design freedom and has revolutionized industries ranging from aerospace to healthcare. - Material Considerations:
The thinnest achievable prints depend heavily on the material used. Different materials have varying properties, including their viscosity, flowability, and structural integrity. For example, thermoplastics like PLA and ABS are commonly used in desktop 3D printers and can produce thin prints with a minimum thickness of around 0.1 mm. On the other hand, metals such as titanium or aluminum require more advanced techniques and can achieve thicknesses as low as 0.02 mm. - Printer Resolution and Nozzle Size:
The resolution of a 3D printer plays a crucial role in determining the minimum achievable thickness. It is defined by the size of the printer's nozzle and the precision of its movement. Smaller nozzle sizes enable finer details and thinner layers. High-end printers with nozzle sizes as small as 0.1 mm can achieve remarkable thinness, while consumer-grade printers typically have nozzle sizes ranging from 0.4 to 0.6 mm. - Structural Integrity and Support Structures:
As the thickness of a 3D print decreases, maintaining structural integrity becomes increasingly challenging. Thin prints are more prone to warping, deformation, or even collapse. To overcome these challenges, support structures are often used to provide stability during the printing process. These structures can be removed afterward, leaving behind the desired thin object. - Application-Specific Considerations:
The minimum thickness for 3D printing varies depending on the intended application. For decorative or artistic purposes, extremely thin prints may be desirable. However, functional parts or prototypes require a balance between thinness and strength. Engineers and designers must carefully consider the mechanical properties and stress distribution to ensure the printed object can withstand the intended use. - Advancements and Future Possibilities:
The field of 3D printing is constantly evolving, and researchers are continuously pushing the boundaries of what is possible. With ongoing advancements in materials, printer technology, and software algorithms, the minimum achievable thickness for 3D printing is likely to decrease further. This opens up exciting possibilities for applications in microelectronics, biomedical devices, and other cutting-edge industries.
Conclusion:
In conclusion, the thinnest you should 3D print depends on various factors, including the material, printer resolution, and intended application. While current technology allows for prints as thin as 0.02 mm in certain materials, it is essential to consider the structural integrity and practicality of ultra-thin prints. As the field of 3D printing continues to advance, we can expect even thinner prints and new opportunities for innovation. So, keep exploring, experimenting, and pushing the boundaries of what is possible in the world of 3D printing!