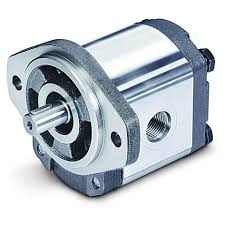
Understanding Gear Pump Technology: Design, Operation, and Applications
In fluid handling systems where precise flow control, compact design, and reliable performance are essential, gear pumps have established themselves as one of the most trusted and widely used positive displacement pump technologies. These compact workhorses are found in a range of industries, from hydraulic systems and chemical processing to food manufacturing and automotive lubrication.
In this blog, we explore the fundamentals of gear pump technology—how they work, their design variations, advantages, and the diverse range of applications they serve.
What Is a Gear Pump?
A gear pump is a type of positive displacement pump that uses the meshing of gears to transfer fluids. It operates by trapping fluid in the cavities between gear teeth and the pump casing, then moving it from the inlet side to the outlet side. Unlike centrifugal pumps that impart velocity to fluid, gear pumps deliver a steady, pulseless flow that is directly proportional to the speed of the driving motor.
Gear pumps are especially favored for their simplicity, reliability, and ability to handle high-viscosity fluids with consistent flow rates.
Types of Gear Pumps
Gear pumps generally fall into two main categories: external gear pumps and internal gear pumps. While they share similar operating principles, each type has distinct characteristics that make them suitable for different industrial environments.
1. External Gear Pumps
This is the most common type, consisting of two identical gears that rotate against each other—one being powered (the drive gear) and the other idling (the driven gear). Fluid is trapped between the gear teeth and the casing, then transported to the discharge side.
Key Characteristics:
High pressure output (up to 3000 psi or more)
Precise metering and dosing capabilities
Bi-directional flow possible
Compact design with tight tolerances
2. Internal Gear Pumps
An internal gear pump uses two gears of different sizes—one inside the other. The smaller internal gear (rotor) sits off-center within a larger external gear (idler), and a crescent-shaped spacer fills the void between them.
Key Characteristics:
Smooth, quiet operation
Better suited for high-viscosity fluids
Ideal for shear-sensitive materials
Often used in food, cosmetics, and chemical industries
Core Components of a Gear Pump
Understanding the basic anatomy of a gear pump helps explain its function and efficiency:
Housing/Casing: Encases the gear mechanism and maintains the pressure boundary.
Drive Gear: Powered by a motor, it engages the idle gear to rotate and create suction.
Driven Gear: Moves in sync with the drive gear to assist in fluid displacement.
Shafts and Bearings: Ensure stable rotation and support gear alignment.
Seals: Prevent leakage and maintain internal pressure.
Materials used for these components vary depending on the application and fluid type—common materials include cast iron, stainless steel, bronze, and engineered plastics.
How Gear Pumps Operate
The operation of a gear pump is based on positive displacement. As the gears rotate, they create a void at the inlet where fluid is drawn into the pump chamber. The fluid is then trapped in the space between the gear teeth and the housing and carried around the gears to the outlet side. There, the meshing of the gears forces the fluid out at a high pressure.
Since gear pumps do not rely on centrifugal force, they are especially effective in handling viscous or non-Newtonian fluids that would be difficult to move using other pump types.
Advantages of Gear Pump Technology
Gear pumps offer several advantages that make them ideal for demanding industrial applications:
Consistent, pulseless flow: Ensures steady dosing and metering
High-pressure capability: Suitable for hydraulic and lubrication systems
Self-priming: No need for external priming mechanisms
Durable and compact: Simple design with few moving parts
Wide fluid compatibility: Handles a broad range of viscosities and chemistries
Bi-directional flow (in many models): Allows flexible installation and control
Limitations to Consider
While gear pumps are incredibly versatile, they also come with a few design limitations:
Not ideal for abrasive fluids: Can cause gear wear and performance loss
Tight clearances required: Limits the ability to pump large solids
Flow rate proportional to speed: May require variable speed drives for control
Internal leakage: Can occur over time with wear, reducing efficiency
Proper pump selection, routine maintenance, and using materials suited for the application are critical to ensuring long-term reliability.
Common Applications of Gear Pumps
Gear pumps are a preferred solution across many industries due to their adaptability and performance characteristics. Here are some notable applications:
1. Hydraulic Power Systems
Gear pumps are widely used in mobile and industrial hydraulic systems to generate consistent flow and pressure. They provide reliable power to actuators, cy
linders, and hydraulic motors.
2. Chemical Processing
Corrosion-resistant gear pumps are ideal for accurately metering chemicals like acids, solvents, and polymers in controlled environments.
3. Food and Beverage
Internal gear pumps are often chosen for transferring viscous food products like chocolate, syrup, honey, or cooking oil while maintaining hygiene and preventing shear damage.
4. Lubrication Systems
In industrial machinery, gear pumps are used for circulating lubricants under pressure to reduce friction and heat buildup.
5. Fuel Transfer
Diesel, gasoline, and biofuels are efficiently transferred using gear pumps due to their pressure-handling capacity and material compatibility.
Recent Innovations in Gear Pump Technology
Modern gear pump designs have evolved to meet the growing demands for precision, energy efficiency, and reduced environmental impact. Some innovations include:
Digital flow monitoring and control for precise automation
Magnetically coupled gear pumps for leak-free operation in sensitive environments
Advanced coatings and materials to reduce friction and wear
Integration with smart manufacturing systems for predictive maintenance
These advancements continue to expand the role of gear pumps in next-generation fluid handling applications.
Conclusion
Gear pumps may seem mechanically simple, but their role in modern industry is both critical and complex. Their ability to deliver precise, high-pressure flow makes them invaluable across a wide spectrum of sectors—from manufacturing and automotive to food processing and energy systems.
Understanding the types, components, and performance characteristics of gear pumps empowers engineers and procurement specialists to make informed decisions that enhance system efficiency and reliability.
If you are exploring high-performance gear pump solutions for your operation, consult AJA Technology and we can provide a reliable solution based on your specific needs (fluid type, pressure range and operating environment).
www.aj-motor.com
Shanghai AJA Technology Co., Ltd.